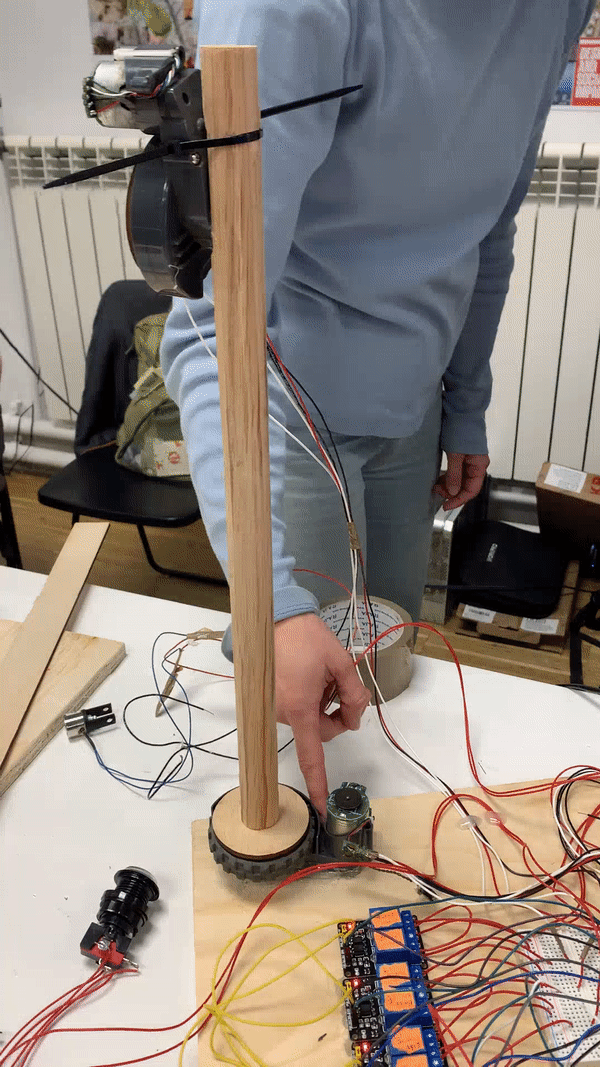
Almost Useless Machines
First sketches
The bazaar.
There was a moment we called “the bazaar” when we could choose pieces of junk to be used in our project. Many of the materials consisted of components from the old electronic appliances we took apart last week, but there were also a few new sensors or electronic components too. The idea was to prioritize the use of scrap materials, and rethink what could be done with them.Jeremy's electronics diagram which I transcribed onto my iPad.
me polishing up the final set using my mini broom
Me, Julia, Gerda, Angel and Jeremy
The final presentation can be viewed here. (you may need to log in with your IAAC email)